PDCA Cycle Explained: 4 Steps for Continuous Improvement
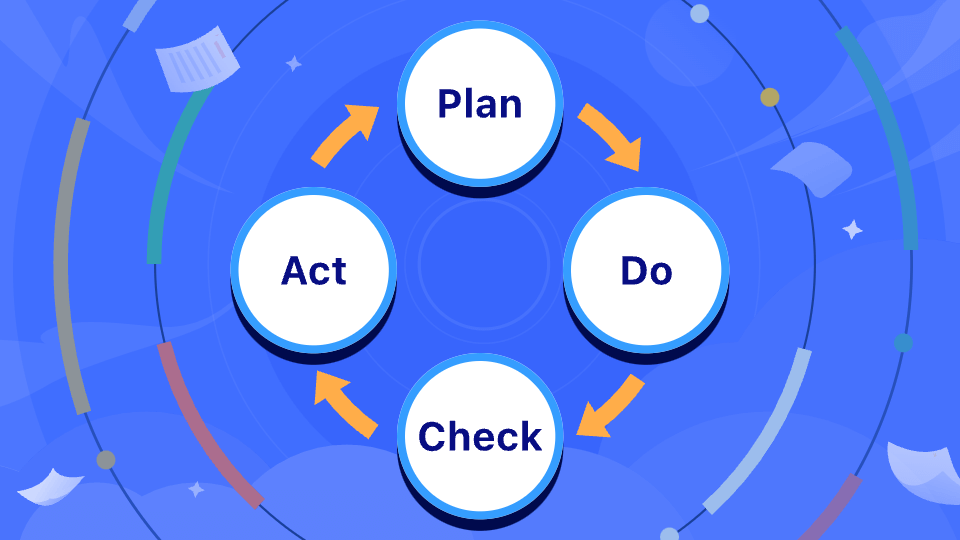
PDCA stands for Plan, Do, Check, and Act, also known as the PDSA or Deming Cycle. It is a problem-solving method used for the continuous learning and improvement of a process or product.
Learn the 4 steps of the PDCA cycle (Plan-Do-Check-Act) for continuous improvement and how to integrate it with TickTick for better productivity.
4 Steps of the PDCA Cycle
There are 4 basic steps in PDCA Cycle:
-
Plan: identify a problem and possible solutions
-
Do: execute the plan and test the solutions
-
Check: evaluate the results and lessons learned
-
Act: improve the plan/process for better solutions
These four steps incorporate inductive-deductive interplay and have been a simple and scientific approach for problem-solving (process-improving). It follows the curve of how we acquire knowledge through constant reflection, standardization, and modification.
Step-by-Step Breakdown
The PDCA framework begins with a planning phase where a problem or a process to be improved is identified. This involves not only the goal setting and finding possible solutions, but also hypothesizing methods that can be used to reach the ultimate goal. Another thing that needs special attention is defining the success metrics. This means establishing a clear evaluation matrix in advance.
Then, the solutions will be tested in the Do process. To detach the Do, there could be two steps: making the Do multiple To-Dos by splitting the task and defining them with a specific time, personnel, and steps, and collecting real-time data and feedback.
Check includes analyzing the results and comparing them to the hypothesis in the Plan stage: how well the solution worked, how much the goal has been achieved, and whether the methods were proven feasible. If there are any unexpected issues, you may also need to find the causes and possible solutions. Note that there might be a forth and back between Do and check.
The Act step closes the cycle, which involves adjustment on the initial goal or solutions and integration of all key learnings by the entire process, to standardize successful parts and avoid error recurrence. In a nutshell, the Act phase summarizes the current cycle and prepares for the next.
However, the PDCA cycle doesn’t stop here. Instead, it can repeat from the beginning with a modified version of the Plan. There is no end to it and sustainability should be its main pitch.
History of the PDCA Cycle
Usually used interchangeably with "PDSA Cycle", "Deming Cycle", "Deming wheel", "Shewhart Cycle" etc, the PDCA model has indeed confronted some misunderstanding and confusion. It remains unexplained in most cases how PDCA became what it is today and what’s the difference between those mysterious terminologies and how they interact. According to Ronald D. Moen & Clifford L. Norman, its evolution could be summarized like the following:
Shewhart cycle (1939): Specification - Production - Inspection. He brought up this method from the viewpoint of Quality Control.
Deming Wheel (1950): Design the product - Make the product - Sell it - Test it. Deming built off the Shewhart cycle and emphasized the four steps should be rotated constantly to aim for the product quality. This has gained increasing popularity when Deming participated in the Japanese Union of Scientists and Engineers (JUSE).
PDCA Cycle (the 1950s): Plan - Do - Check - Act. A Japanese executive reworked the Deming Wheel and translated it into the PDCA Cycle for problem-solving. PDCA emphasizes more on the establishment of standards during the process and the ongoing modification of those standards.
Extended PDCA Cycle (1985): Plan - Do - Check - Act. Kaoru Ishikawa refined the PDCA model to include more steps in the Plan and Do steps: Identify the goals and methods to use; involve in training and education during implementation.
PDSA Cycle (1985): Plan - Do - Study - Act. Deming claimed that the ownership of PDCA Cycle was never recognized by anyone and the word "check" was used incorrectly because it means "to hold back". Therefore, he replaced it with "study" to emphasize the importance of the continuous learning-improvement model.
Benefits of PDCA Cycle
Among all those other methods, why does the PDCA model shed some light in history, especially known for the "Japanese Quality" and is still widely used today? Some key benefits of it need to be valued.
Continuous improvement and adaptability: PDCA methodology emphasizes minimizing errors and maximizing results. When applied to business development, e.g. a product’s iterations, it could ensure a developing path where the product is shaped better and better to the market and customers. It’s the same when it comes to personal growth. By consistently planning, doing, checking, and acting, you can refine your work methods, resulting in enhanced efficiency and improved outcomes.
Learning curves and knowledge acquisition: PDCA framework follows a learning curve and enhances the learning-improvement process continually. This is the key factor defining PDCA as a scientific and methodical way to gain knowledge. Through continuous learning and improvement, your knowledge and abilities will steadily enhance.
Fostering a growth mindset: PDCA model encourages a growth mindset. By consistently refining your work methods, you can boost your self-esteem, cultivate a sense of achievement, discover significance in both work and life, and avoid stagnation.
Implementing the PDCA Cycle
Integrating the PDCA (Plan-Do-Check-Act) cycle with TickTick can streamline your workflow and enhance productivity. Here’s how you can effectively use TickTick to implement the PDCA cycle:
Plan
Planning is the cornerstone of the cycle, laying the groundwork for subsequent actions. During this phase, establish your work objectives and task plans.
-
Add tasks: Populate your task list with all the tasks you need to complete. Use the SMART principle and subtasks or checklists to break down complex tasks into manageable steps. For example, if your main task is "Write a market analysis report", subtasks could include "Gather market data", "Analyze market trends", "Write the report", etc.
-
Set priority and deadline: Utilize TickTick's priority feature to rank tasks by importance. Then, assign deadlines to each task based on priority, ensuring a clear timeline for your plan.
Do
Simply execute tasks according to the plan in this step. Here are some helpful suggestions for maintaining focus:
-
Set reminders: Ensure task completion by setting reminders for each item.
-
Use the Pomodoro Technique: Use TickTick's Pomodoro timer for 25-minute work intervals followed by a 5-minute break, aiding in task concentration and distraction avoidance.
-
Use the Eisenhower Matrix: With the Eisenhower Matrix, you can visually see the most important tasks of the day, ensuring a productive start by tackling the most crucial tasks first.
Check
Check task execution status and assess plan goal achievement. Ask yourself: What are the issues if execution falls short of expectations? What aspects can be maintained if execution is successful?
-
Create a checklist: Establish a "Check" note list for review and replay. Record evaluation goals and results in this list.
-
Record check results: Summarize task completion and data periodically in note comments, comparing actual outcomes with plan expectations. Utilize TickTick's markdown feature to document feedback and issues encountered during the check process.
Act
Based on the check results, summarize lessons learned and implement necessary improvements.
-
Develop a new plan: Adjust plans based on check feedback. For instance, reduce daily task quantity if overestimating energy levels.
-
Start the next cycle: Implement improvement measures in the next cycle for application and validation.
The PDCA cycle is an invaluable tool for anyone seeking continuous improvement in both professional and personal contexts. By adopting this systematic approach to problem-solving, you can drive consistent growth and achieve measurable results. Use TickTick to seamlessly integrate the PDCA cycle into your daily workflow and start experiencing better productivity and efficiency today.